26/08/2021
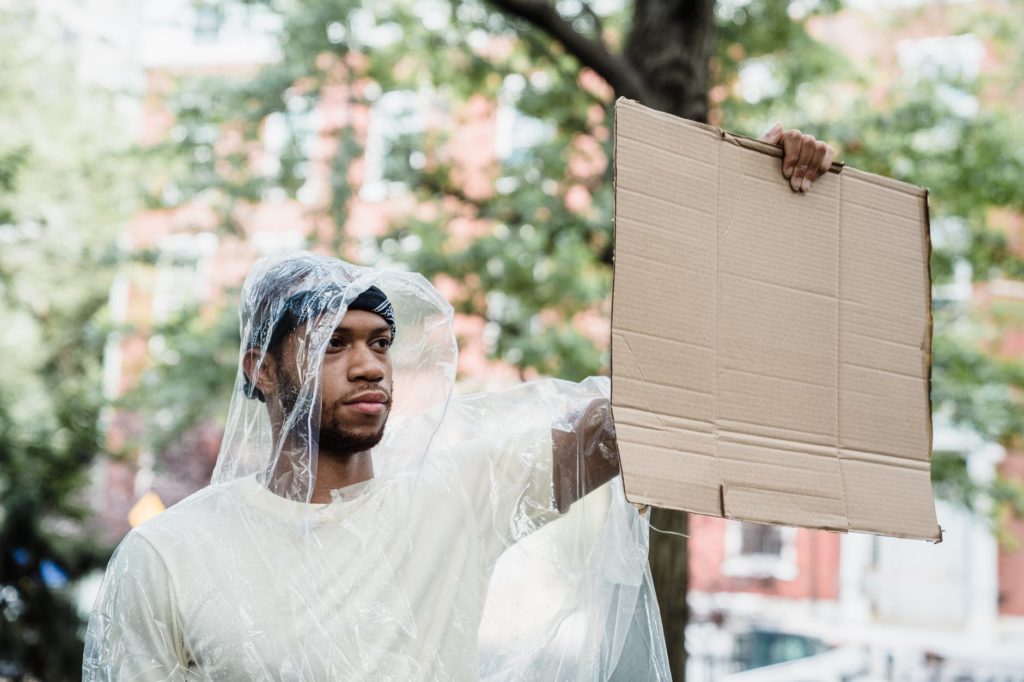
Simply Wrapped – The Triumph of Monomaterial Packaging
Packaging often leaves consumers puzzled. You’ve just finished a delicious pizza and are on your way to the recycling bin with the empty box, when questions about proper waste separation start popping up. There’s this thin aluminum layer on the inside. Can the paper tube still go into the blue bin? And what about the cheese residue sticking to the bottom? That should really go into the compost. The sticky dairy product definitely doesn’t count as packaging material. What initially looks like cardboard made from renewable material turns out to be a mix of processed milk, aluminum, and cardboard. As such, the packaging material cannot simply be disposed of as paper waste. But where should it go then?
Mono-material packaging must, according to the Federal Environment Agency , be made of at least 95 percent of the main material, such as paper tube in the case of a pizza box. If this percentage is not met, or if multiple materials make up the packaging, it is considered composite packaging. These belong in the yellow bin.
More and more companies are focusing on mono-packaging
There are many examples of this. The drugstore chain DM, for example, uses pure polypropylene for certain toothpaste packaging. This material makes recycling easier, as mixed plastics are more technically challenging to process. Packaging company Antalis also relies on mono-material solutions for its protective packaging. Paper fiber packaging and cushioning molded parts are made 100 percent from paper or cardboard and can be disposed of easily along with the main carton.
From waste to raw material – recycled paper
Ecological mono-packaging made of paper makes an important contribution to sustainability and environmental protection. Only paper can that end up in the paper waste are truly sustainable and can be reused. For this reason, legislation requires that by 2022, 90 percent of primary packaging made from cardboard or paper must be recycled.
Paper is the optimal mono-packaging
Until the 1950s, it was common practice to package food in paper. Then plastic came along and gradually replaced paper. In times of climate change and increasing calls for environmental protection, companies are revisiting paper – including as mono-packaging. However, food requires special protection through packaging, which paper cannot always provide.
For over 100 years, paper packaging has been used for products that only need protection from light, such as flour and sugar. These foods are stored in glued tubular bags that can easily be disposed of in the paper waste. But what can be done to store liquid products like yogurt in paper or cardboard?
On the way to a full-paper solution
Yogurt cups are usually made of plastic or consist of multiple components. Often, there is a thin plastic cup inside, while the printable outer sleeve is made of renewable cardboard. While this allows everything to be sorted neatly into the appropriate bins, the plastic component still poses a residual burden on the environment.
This is why companies like packaging manufacturer Antalis are working on sustainable production of paper packaging that does not require additional components. Yogurt cups made entirely from renewable paper already exist. The inner coating is a thin layer of vegetable starch. Since it is biodegradable, the cup can go into the paper waste.
In 2015, paper manufacturer Billerud Korsnäs developed a system for sealed tubular bags. As the first supplier, they provide sealed paper packaging for dry foods that does not compromise on product protection and dust tightness. By using FSC or PEFC certified paper, this production method aims to offer sustainability from raw material to recycling.
Diverse packaging solutions
Since companies always aim for profitability alongside sustainability, firms like Syntegon Technology are exploring ways to produce paper packaging as quickly and efficiently as plastic wrapping. A breakthrough is the cold sealing of tubular paper bags. Thanks to technical innovations, Syntegon Technology achieved its goal of 800 seals per minute, a performance previously only seen in the plastic industry.
New technologies mean new packaging possibilities and styles. Round, square, or tubular bags—many options are now feasible. Whether Doy packaging or creative innovations in tube form, more and more solutions made of paper and cardboard with barrier and sealing layers are making their way onto store shelves. The packaging industry aims to offer the same variety of mono-paper solutions as with plastic and composite packaging. Then not only the pizza box but also the entire yogurt cup could go into the paper waste.